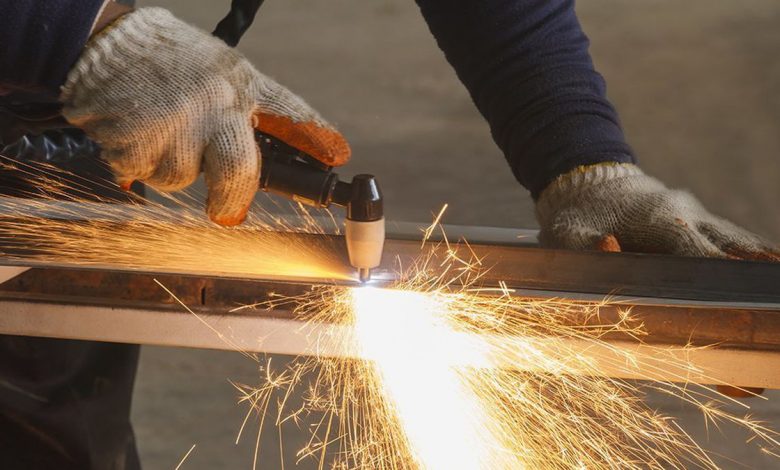
The Basics of Plasma Cutting
Plasma cutting process
Plasma cutting is the fastest process for cutting carbon steel, aluminum, or stainless steel. Plasma cutters can be combined on the same part with a water jet as oxygen fuel.
Top-rated Plasma cutters can be used to accurately cut materials up to 6 inches from stainless steel. Plasma cutting was invented by ESAB in 1955 and we have never stopped developing ways to improve and facilitate plasma cutting. ESAB’s latest innovations in the automation of plasma cutting processes increase production every time with a more constant cutting quality, whatever the skill level of the operator:
Arc plasma
The Web property in Webster is defined as “a set of charged particles. Which contains roughly the same number of positive ions and electrons and certain properties of gas, but which differs from gas in that it is a good conductor of electricity … “
For electric arc cutting, plasma can also be defined as a stream of electrically heated gas. The gas stream is heated to such a high temperature that it is ionized. The ionized gas can then be exchanged electronically freely between atoms. It is the movement of the electron that causes the gas to carry the amplitude of the shift.
Moreover, the plasma torch uses a copper alloy nozzle to limit the flow of ionized gas to concentrate energy in a small diameter. The principle is the same as using a magnifying glass to conduct solar energy and generate intense heat.
The gas flowing through the nozzle also serves as a means to remove heated molten metal from the ionized gas. About 30% of the gas is actually ionized (under optimal conditions) and the remaining 70% of the gas stream is used to recover and cool the material.
Swirling gas
The gas vortex allows cutting in various ways. The vortex increases cooling. Non-ionized gas atoms are heavier / cooler and are forced out of the rotating gas stream. This cold barrier protects the copper nozzle. As the current strength increases, the number of ionization increases (rate of change 30/70%), and the cooling decreases, which shortens the life of the spray board. The nozzles are designed to operate at a certain current (amps).
The vortex improves the cut quality.
If the plasma gas does not work, the damage will occur on both sides of the cut. By changing the gas, the arc is evenly distributed over one side of the cup. If the reverse direction (CW to CCGC) is reversed, the square side changes. When the ionized gas (plasma arc) is ignited, the electric arc is maintained even at the leading edge of the cut. These additional multipliers provide a more even distribution of power over the workpiece. This imbalance of force leads to the square side. The other side with a 5 to 8-degree tilt point.
The introduction of shielding gas limits and further cools the mouthpiece. This gas is injected into the plasma stream after the ionization process at the top of the syringe.
Water injection improves cut quality and cools the nozzle. By swallowing water in the same direction as the gas and injecting where the arc leaves the nozzle, the arc is further restricted. When cold water comes in contact with the high-temperature arc, a vapor layer forms between the arc and the nozzle. The effects of this barrier can be demonstrated by heating the plaster and pouring water. Immediately, small drops of water will dance on the surface of the elbow instead of evaporating. These water droplets are protected by the insulating properties of the vapor that forms when water comes into contact with the container. For water to function properly, the water temperature must remain below 70 ° F. A condition called film bake occurs when the temperature rises above this point. The result is an unstable arc, shorter spray life, and poor cut quality.
Initial plasma arc
There are three main parts to the lamp housing.
- Electrode
- Gas shot (vortex)
- Nozzle
These items are called consumer goods. During the plasma process, it spins over time and needs to be replaced. Some parts of the ESAB PT-36 lamp are shown above. Other flashes may look different, but each has components that serve above as the 3 most important. Consult the burner manual for the correct configuration.
Although, the electrode is connected to the negative side of the DC plasma source. The nozzle is connected to the positive side
When accessing the plasma system for the first time, the following events occur:
- The main switch supplies power by applying a high negative voltage to the electrode.
- The gas begins to flow into the burner and rotates with the plate.
- Close the normally open contacts in the spray circuit and provide a path to the positive side of the power supply.
- The high-frequency generator supplies a high-frequency potential voltage between the electrode and the nozzle. This creates a small spark between the nozzle and the electrode and ionizes the path with the gas.
- On this ionized path, a larger DC arc begins to flow between the electrode and the nozzle. This is known as a pilot arc.
- Unlike,the arc of the fan is blown out of the syringe bladder by a stream of gas and comes into contact with the workpiece.
- The main arc occurs when the arc is transferred to the material to be machined (when the torch is close enough). The spray relays open to remove the nozzle from the circuit. Arc mode is set.
- After opening the spray relay, the primary arc increases to the shear force.
Double arch
A double arc is a condition where the nozzle remains in the plasmid. As described above, the nozzle should only be in orbit during the arc flight phase. If the nozzle is left in the circuit, it has a shear force that destroys it.
The double arch is caused by:
- Pierce gets up. The torch must be positioned close enough to the workpiece so that the visor touches the plate so that it can support the main arc. The drilling current is thrown into the first hole at a slight angle. As the arc moves through the material, the splash becomes more vertical. This word game connects the board and the mouse and keeps the mule in orbit even if the relay is opened and removed. This scenario could damage the front of the flashlight.
- The burner in contact with the plate. Cut the thin material. All automatic torch positioning systems use an initial height measurement to position the torch on the plate. Indeed, one of the methods is the method of recovery. The flashlight moves until it hits the board and returns to the first starting height with a timer or code. If the contact is not observed correctly, the torch may still be in contact with the material due to the material breaking or shrinking. The nozzle remains in the plasma circuit with sheer force and causes damage.
- Pilot arc error. This can occur if the current from the pilot arc relay does not remove the nozzle. This can be done with a short relay as a resistor. If the sprayer runs longer than expected, it is damaged.
Avoid double curves
A double arc normally occurs during the drilling sequence.
Some techniques that can prevent double bending are:
- Crawling movement. The cutting machine is programmed at a slower speed to initiate machine motion during arc transfer. This speed is usually 5-10% of the normal cutting speed and is valid for a while. Spray leaks are currently being removed from the spray path. As a result, this reduces the possibility of a double curve.
- The flashlight rises until it penetrates. During the arc transfer, the torch begins to separate from the workpiece. This allows any nozzle sprayer to clean the nozzle. This insertion takes some time and then drops to the correct height of cut after the machine has moved to the cut speed.
- Drill higher than the normal starting height (vertical drilling). This allows splash entry to escape from the nozzle and reduces the risk of a double arc. This prevention method is the least effective.
You can visit our site to read more interesting articles.