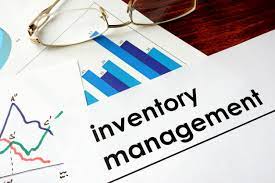
In this complete manual to stock control, you may analyze everything from the definition to the basics of the inventory management system, the methods involved, and a way to cause them to work in a business situation.
What is an inventory?
Inventory is something that you keep. In a retail context, very without a doubt, Inventory refers to your raw material as well as the inventory completed items of merchandise which you sell. It is measured in units of inventory in addition to the price of the stock you preserve.
What are the sorts of Inventory?
For a store, there may be typically the most effective form of stock. This is the product that is prepared for sale.
In the producing industry, inventory is split into 3 essential kinds for ease of accounting. The three kinds are
uncooked material: this consists of all the fabric that you will use to produce a positive product.
Paintings-in-development: this includes all of the parts you manufacture but are but to assemble.
Finished product: as the call shows, this is the assembled product that is prepared for sale. A regular retailer best holds this sort of inventory.
What is inventory/inventory management?
Inventory Management is the technology of purchasing, supervising, controlling, and meting out of Stock for Sale that is saved in a facility. It covers all elements of stock management across the supply chain from the manufacturer to the factor of sale manned via the retailer.
The method of inventory control starts off evolved from the time you boost a purchase order and ends (for every order) whilst an order is fulfilled/ added to the quit consumer. As a store, your task is to control stock smoothly and at as low a fee as viable so you can
- promote the right products
- block the least viable operating capital at all times
- satisfy orders on time so that it will construct client loyalty
- preserve your sales model.
What are the factors of Inventory management?
Inventory Management is a broader topic that covers the following elements:
- A system of naming for your inventory objects (also called Stock Keeping Units, or SKUs)
- Movement of stock from one vicinity to every other
- Purchasing products from Suppliers
- Sale of products to customers
- Frequent evaluation and adjustment of Inventory
- A usual discount on deadstock
Efficient Inventory Management is important for manufacturers, retailers, and types because it’s miles how they treat their core business and extract value from the method of purchasing and promoting.
Why is Inventory Management essential?
You may have often questioned why you even have any inventory in any respect. Is it not simply less difficult to ask a dealer to ship your products as and if you have some demand for them? The issue, but, lies in the reality that we by no means understand for sure what a consumer’s spending sample is.
For example, it’s miles feasible that your producer can not preserve up when your call for peaks. Or your dealer may additionally boom the rate of a product you agreed to sell for way lesser.
Having your own inventory enables a hedge towards the exceptional uncertainty this is customer behavior. When you buy in bulk, you furthermore might have a bonus when it comes to price negotiations. Moreover, you can appreciably lessen the time between order and delivery by having your own inventory.
Key Inventory Management Terms You Need To Know
Well, as a minimum it is able to appear like jargon, but these terms which are casually thrown around in inventory management let you understand better.
1. Maximum Stock Level
As the name implies, that is the level of inventory indicated with the aid of a number of past which you honestly shouldn’t stock up on a specific product. This range is inspired by several elements- the perishability of products, the quantity of warehouse space you’ve got, changes in client alternatives, and so forth.
2. Minimum Stock Level/Safety Stock
This is absolutely the minimal range of merchandise you need to have so one can satisfy marketplace demand.
Lead time is the quantity of time it takes in an effort to acquire a product from the vendor. From the time which you’ve located an order for it. Another factor that influences the Minimum Stock Level is the charge at which your product is being offered throughout the lead time.
3. Reorder Level
This range represents the point at which you have to increase a reorder request from your vendor. So one can make sure that you stay above the minimum inventory degree.
4. Reorder Point
In the best of phrases, the reorder point is that factor in time when you want to reorder inventory for a product. To avoid the threat of walking out of stock. The crude way to try this would be to preserve a watch for your stock and order on every occasion its miles coming close to being over.