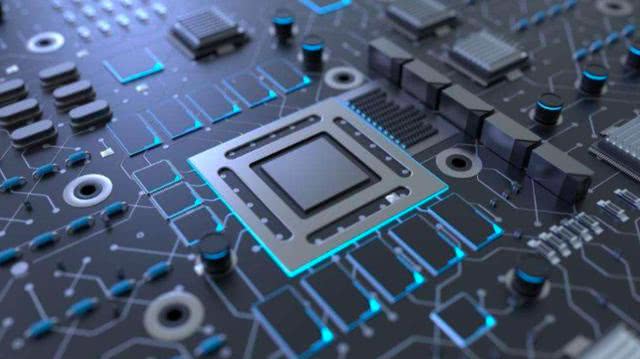
As early as the second half of last year, the semiconductor industry suffered a supply shortage of chips. Although the chip factory operates around the clock, the world semiconductor at this time is still facing the danger of chips shortage.
In the near future, this “carnival” about chips shortages will surely dissipate. But at this moment, the industry’s “fishy storm” is still going on. The global supply of automotive semiconductors is insufficient, and major automakers have announced production cuts. Then the chip prices continue to rise, and panic buying is not uncommon.
Why is there a global shortage of semiconductors? Today, I will discuss with you the “semiconductor industry in change” from the subdivision of semiconductor chip manufacturing.
Why is there a global shortage?
Insufficient supply of chips is closely related to the breakdown of the balance of supply and demand. During the epidemic, the demand for home appliances (such as Nintendo game consoles, smart home appliances, smartphones, etc.) increased, and the demand for semiconductor chips also increased. The increasingly popular electric vehicles have greater demand for semiconductors. As the epidemic is under phased control, major automakers will expand production.
However, the start of the Sino-US trade war broke the stable cooperation model of the semiconductor global supply chain. In recent years, the US government has imposed a blockade on China’s semiconductor industry. Major semiconductor manufacturers in Europe, America, and even Japan have moved their foundry manufacturers from mainland China to Taiwan and other regions.
Industrial structure and production mode of chip production
In order to understand the root cause of this chips shortage crisis, let’s first briefly understand the industrial structure and production mode of chip production. Simply put, the semiconductor chip industry consists of upstream design and development, downstream production, packaging, and testing.
Semiconductor manufacturers in the world today are roughly divided into two modes:
One is a vertical enterprise that covers the design and development department. It has a production plant, also known as (IDM mode). Representative companies include Intel (U.S.), Renesas (Japan), Samsung (Korean), etc.
The other is to perform their duties. The design and development companies (Fabless) and the production companies (Foundry) are independent of each other, but they cooperate with each other to form a horizontal division of labor mode, also known as the Fabless&Foundry mode. The United States is an absolute leader in design and development companies. Representative companies include Broadcom (U.S.) and Nvidia (U.S.), while the main force of production companies (Foundry) is concentrated in Asia, especially China and Taiwan. Representative companies are SMIC (Mainland China) and TSMC (Taiwan).
Vertical semiconductor company VS horizontal division of labor
Which one is better between vertically operating enterprises and horizontal division of labor has always been a topic of debate in the industry. However, in the semiconductor world for more than 20 years, horizontal division of labor enterprises have made considerable progress.
Due to the upgrading of semiconductor application products, the separation of development, design, and manufacturing is more conducive to field specialization and business flexibility. The concept of Open Innovation is also deeply rooted in the semiconductor industry.
In 2010, in the top 10 global semiconductor companies ranking list, only Broadcom and Qualcomm were on the top 10 ranking of global semiconductor companies, and the two companies were on the list, and the list was at the bottom. By 2020, the horizontal division of labor has occupied half of the list. The overall ranking has risen year by year.
Therefore, the horizontal development of the semiconductor industry has prompted the strong rise of downstream foundries. TSMC and SMIC, as its representatives, shoulder the responsibility of global semiconductor chip front-end production.
The excessive development of the horizontal division of labor-the source of the crisis of the global shortage of semiconductors
More and more chip companies are choosing a more flexible horizontal division of labor, putting their main focus on development and design, while the production and packaging aspects are given to Asia. The Sino-US trade war started. Major semiconductor design and development manufacturers in Europe, America, and Japan transferred a large number of foundry production orders from mainland China to Taiwan, resulting in a serious shortage of production capacity of manufacturing companies such as TSMC. This has led to major design and development companies in the world. The factory will be “out of stock” situation.
A small number of foundry manufacturers are now like a faucet in the desert, dripping water slowly. A large semiconductor design and development factory is like a hungry crowd waiting in line. At first, they waited in line; later they simply raised the price to buy; then they became impatient.
Summary
The global shortage of semiconductors this time is unprecedented and has a far-reaching impact. It seems to pierce the nerves of every semiconductor person deeply. Especially in Japan, the supply chain model of Just in time is highly sought after. The Japanese act cautiously and keep inventory on demand, thereby reducing inventory pressure and costs. But this time the semiconductor shortage has completely destroyed the superiority of Japanese companies’ systems. With shortages, long delivery periods, and insufficient semiconductor inventories, most companies are immersed in the crisis of “exhaustion of ammunition and food.”
Semiconductor manufacturers, even if they are running at full power and producing around the clock, cannot fill the huge black hole of insufficient supply. At this time, the major design and development companies racked their brains, trying to get a share of the promised mass production from the foundry giants. Behind the scenes, they are quietly looking for “foundry spare tires”, or simply exploring the road of independent production. In the semiconductor industry, we are also experiencing this “war” without gunpowder.